I have worked in the Kenyan construction sector long enough to know one thing—whenever a contractor says, “We are using local materials,” it’s either a lie or a warning that trouble is coming. The government keeps preaching the gospel of Buy Kenya, Build Kenya, but on the ground, where bricks hit mortar, things are different.
Anyone who has spent time on a construction site will tell you this: Kenyan-made materials have a reputation problem. Not because we can’t produce quality, but because the system is wired to make imported materials the default choice. Let me explain.
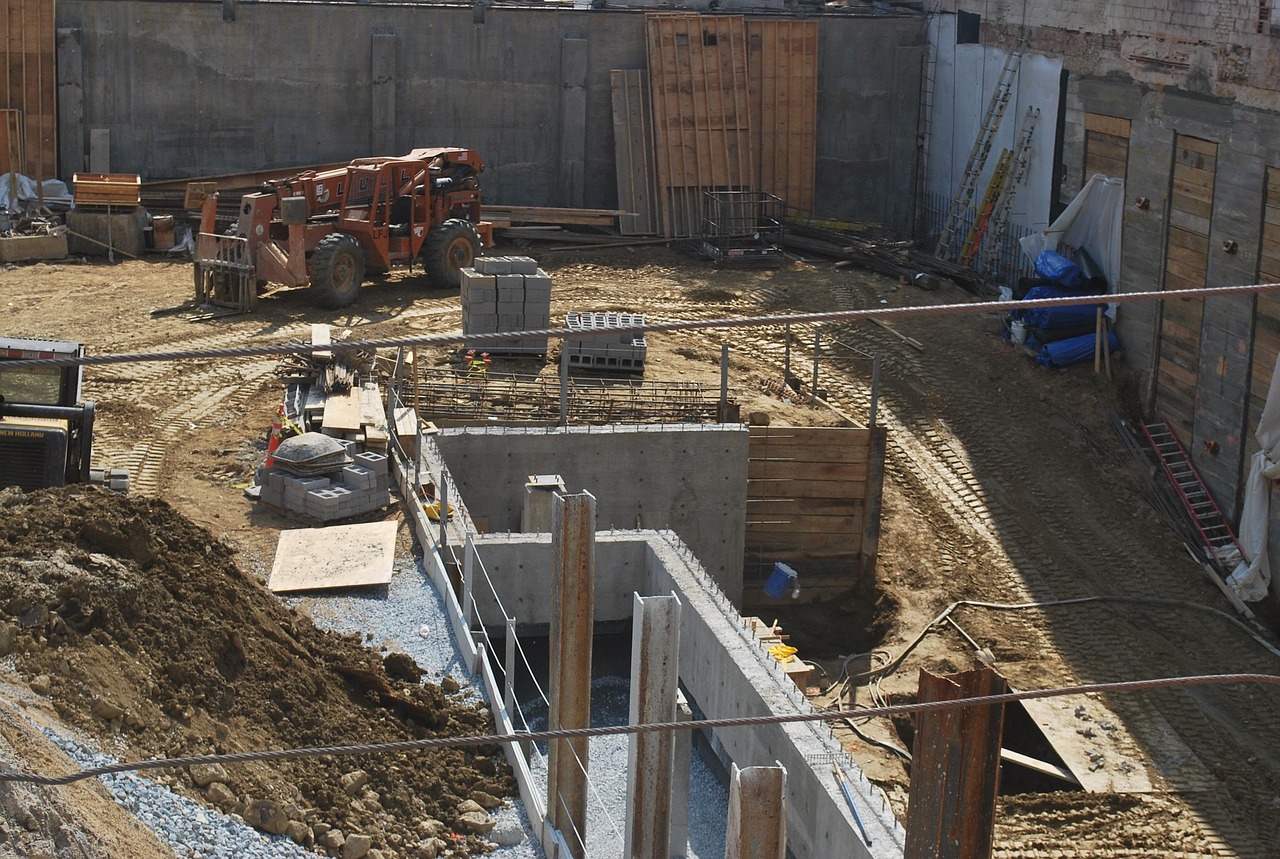
Why Do Contractors Avoid Local Materials?
Let’s start with the basics—cement, steel, and roofing sheets. In theory, Kenya has several well-known cement manufacturers. Yet, walk into a hardware store, and you’ll hear whispers of “imported cement is stronger.” Some clients demand brands from Egypt or China, convinced that what’s made locally is substandard. But why?
For years, Kenyan manufacturers have struggled with inconsistent quality control. One batch of locally made steel bars might be perfect; the next might fail stress tests. Roofing sheets from a factory in Thika might work well on one project but rust prematurely on another. Construction is a high-stakes industry—no one wants to gamble with materials that might let them down.
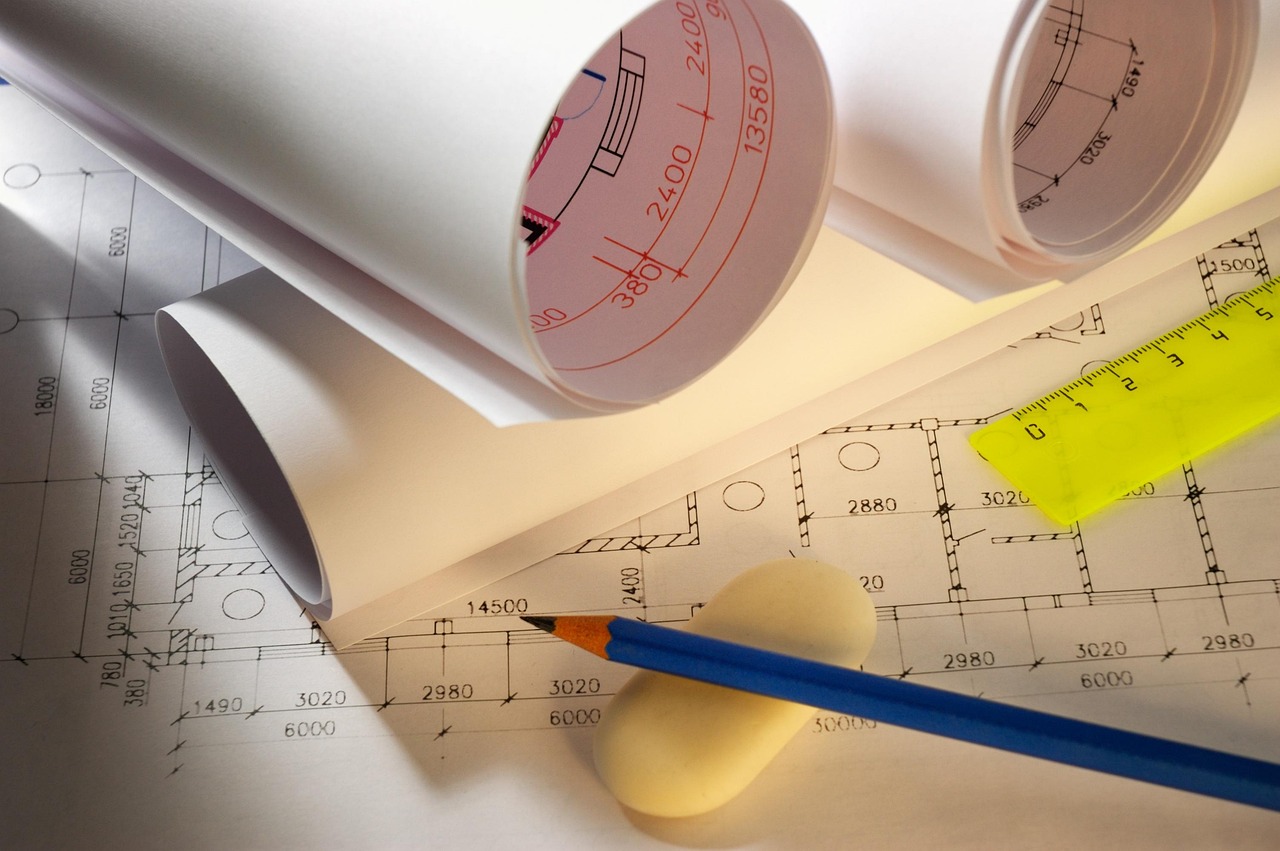
The Cost Paradox: Why Local is Expensive
You’d think that materials made within our borders should be cheaper than imports. But here’s the twisted reality: locally made construction materials often cost the same—or even more—than their imported counterparts.
Why? Corruption, taxation, and logistics.
Manufacturers are hit with high production costs, thanks to expensive electricity, unpredictable fuel prices, and a never-ending list of levies. By the time a bag of Kenyan-made cement reaches a construction site in Kisumu, it might cost more than cement shipped all the way from Pakistan.
Meanwhile, cartels in the importation business ensure foreign materials flow in smoothly—sometimes even avoiding taxes altogether. When a truck carrying imported steel “accidentally” bypasses customs, who suffers? The local manufacturer, who must play fair and pay the full cost of doing business.
Fake Products Flooding the Market
Ask any fundi about counterfeit building materials, and you’ll hear horror stories. Kenyan stores are packed with low-quality knockoffs masquerading as genuine local brands. You buy “Kenyan steel” for a reinforcement job, only to realize it bends like wet sugarcane. The paint you thought was top-quality starts peeling after two months.
Without strict enforcement of quality standards, local manufacturers lose credibility. And once trust is gone, it’s nearly impossible to regain.
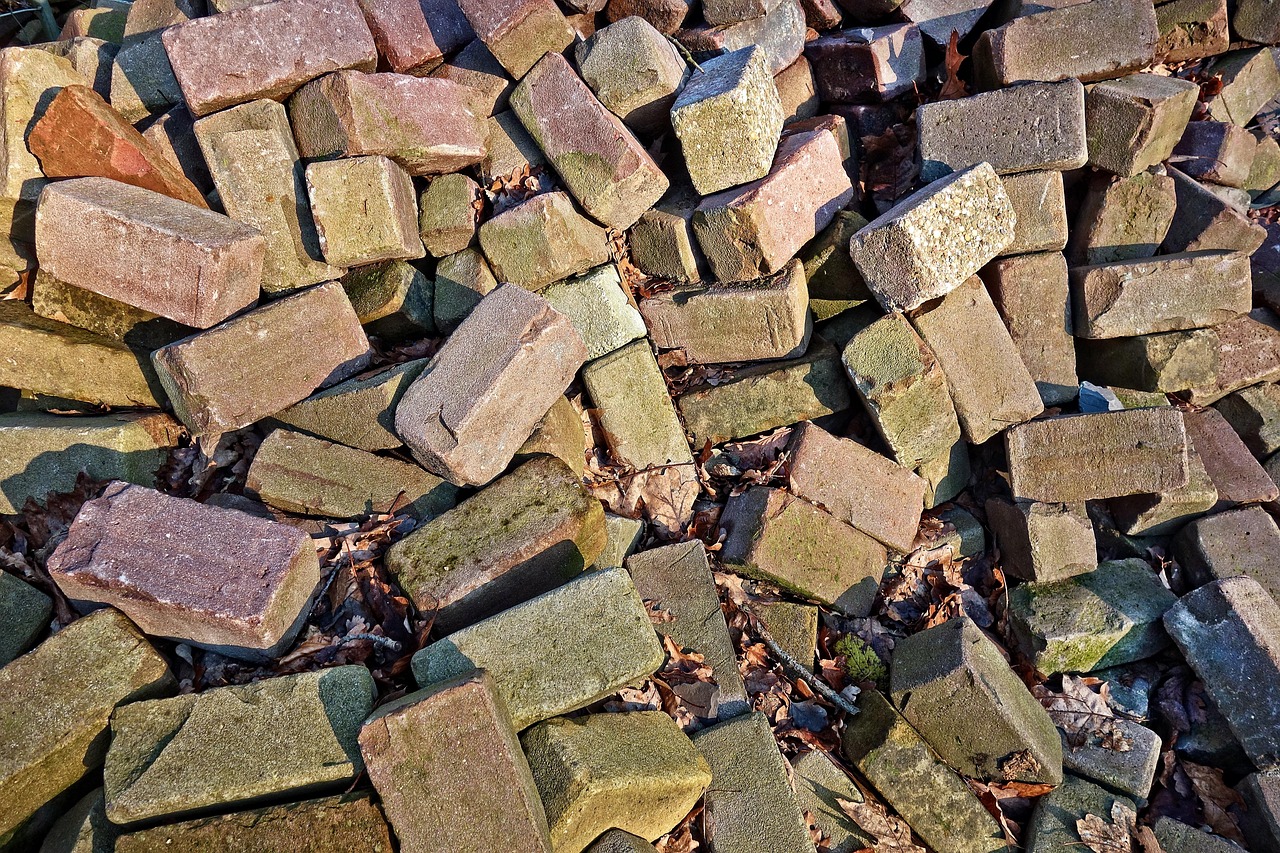
The Imported Mindset
Beyond economics, there’s a deeper issue—perception. Many Kenyans believe that anything imported is superior. Even when local products match or exceed international standards, there’s a silent bias: If it’s foreign, it must be better.
Contractors, architects, and developers reinforce this mindset. When a client is paying millions for a house, they want “the best.” If that means buying Italian tiles instead of Kenyan ones, so be it.
Can We Fix This?
Absolutely. But it won’t be easy.
- Strict Quality Control: The government must crack down on substandard local production. If a Kenyan company makes nails today, those nails should be just as strong next year. Consistency is key.
- Fair Trade Policies: If imports are allowed to flood the market duty-free, local manufacturers don’t stand a chance. We need a level playing field, where Kenyan products compete fairly without being strangled by unnecessary taxes.
- Mindset Shift: We must change how we view our own products. If South Africa can proudly use its own cement and steel, why can’t we? Our engineers, contractors, and architects need to lead this cultural shift.
- Crackdown on Fakes: Counterfeit building materials shouldn’t exist in a country serious about development. If a company is found selling fake Kenyan cement, it should be shut down immediately.
Final Thoughts
Kenya has the potential to produce world-class construction materials. But for now, Made in Kenya remains a promise—one that’s yet to be fully realized. If we don’t fix this, we’ll keep importing materials we could have made ourselves, sending billions overseas while our own industries struggle.
And for those of us on the ground—construction workers, foremen, and contractors—we’ll keep waiting for the day when local means quality.
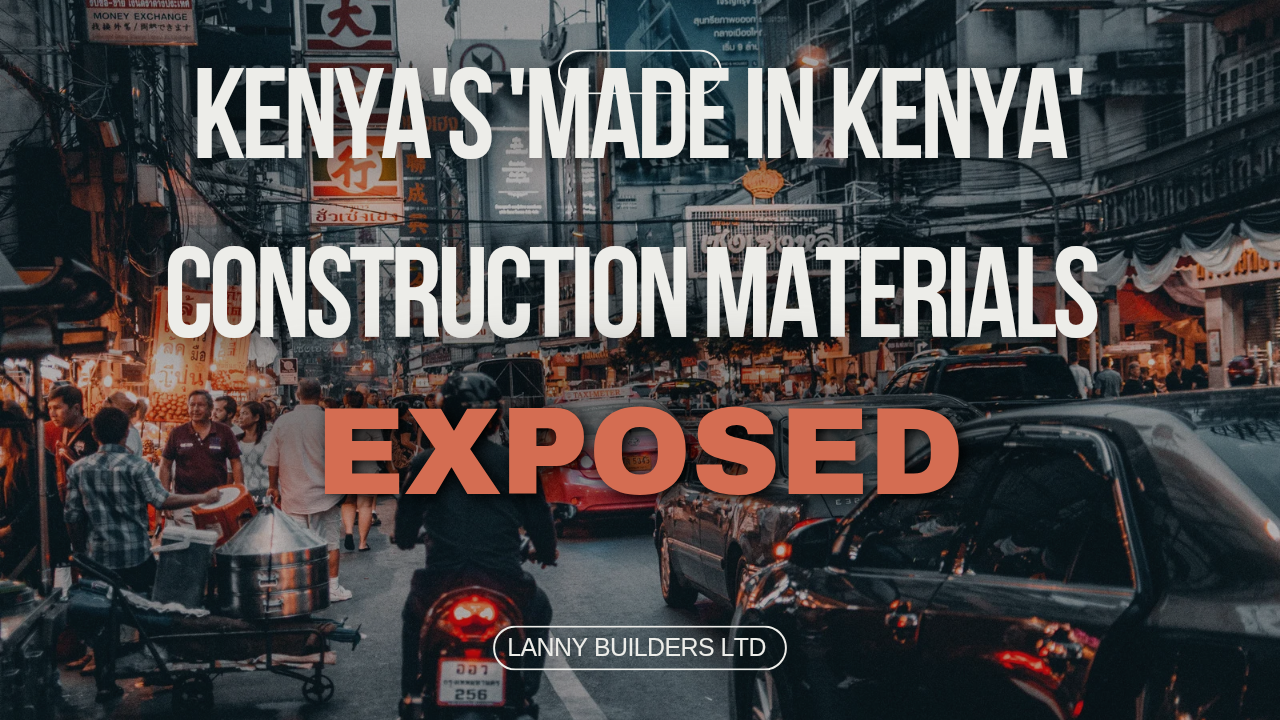