The Rise of Modular Construction: Building Smarter, Faster, and More Sustainably
In the ever-evolving world of construction, one approach is changing the game: modular construction. It’s not just a buzzword anymore; it’s a transformative method reshaping how buildings are designed, constructed, and delivered. If you’re unfamiliar with modular construction, here’s the gist: entire sections of a building are manufactured off-site in controlled factory environments and then assembled like puzzle pieces on the final site. Think of it as Lego blocks for the real world—only much more sophisticated.
But why all the hype?
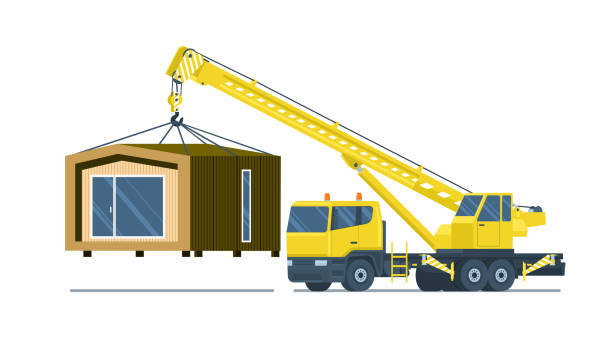
What Makes Modular Construction Stand Out?
Traditional construction methods often face challenges like delays, weather disruptions, and material wastage. Modular construction, on the other hand, offers a host of advantages:
- Speed of Construction:
Imagine cutting construction timelines in half. Because modules are built simultaneously in a factory while site preparation happens elsewhere, projects are completed faster. For developers and contractors, this means quicker returns on investment. - Enhanced Quality Control:
Unlike open-site construction, factories offer a controlled environment. This ensures precision, consistency, and adherence to strict quality standards. It’s like comparing a hand-stitched suit to one made in a modern textile factory—both good, but one is far more consistent. - Sustainability in Action:
The construction industry is notorious for generating waste. Modular construction minimizes waste by using exact measurements and recycling leftover materials. Plus, transporting ready-made modules reduces the energy spent on-site, contributing to a smaller carbon footprint.
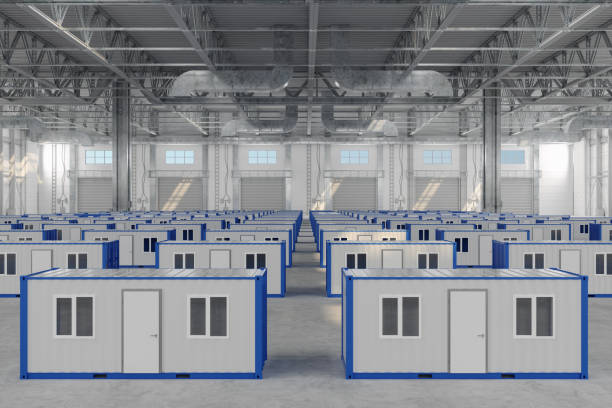
Applications Beyond Housing
When people think of modular construction, they often imagine housing projects. While it’s true that modular homes are booming, this method is making waves in several unexpected areas:
- Healthcare Facilities: Temporary hospitals, such as those built during the COVID-19 pandemic, were erected using modular methods to meet urgent demands.
- Education: Schools and universities are turning to modular classrooms for quick expansions without disrupting ongoing activities.
- Commercial Spaces: Retailers and restaurants are adopting modular units for pop-up stores and permanent locations, blending speed with innovation.
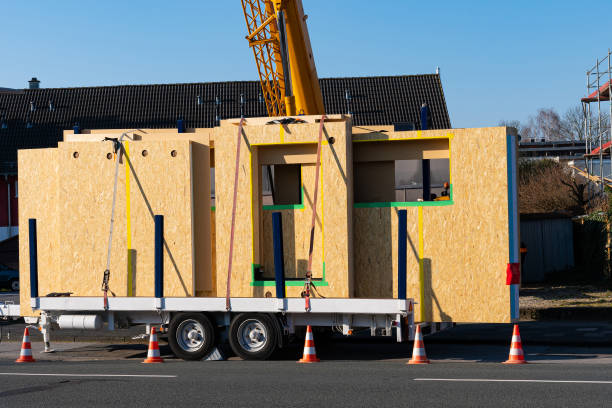
Challenges Modular Construction Faces
Of course, no innovation is without hurdles. Despite its many advantages, modular construction still faces:
- Perception Issues: Some stakeholders associate modular construction with low-quality prefab structures. Overcoming this stereotype requires continued education and successful high-profile projects.
- Transportation Logistics: Moving large modules to remote or urban sites can be tricky. The size and weight often require special permits and routes.
- Initial Costs: While modular construction can save money in the long run, the upfront investment in factory setups or specialized modules can be steep.
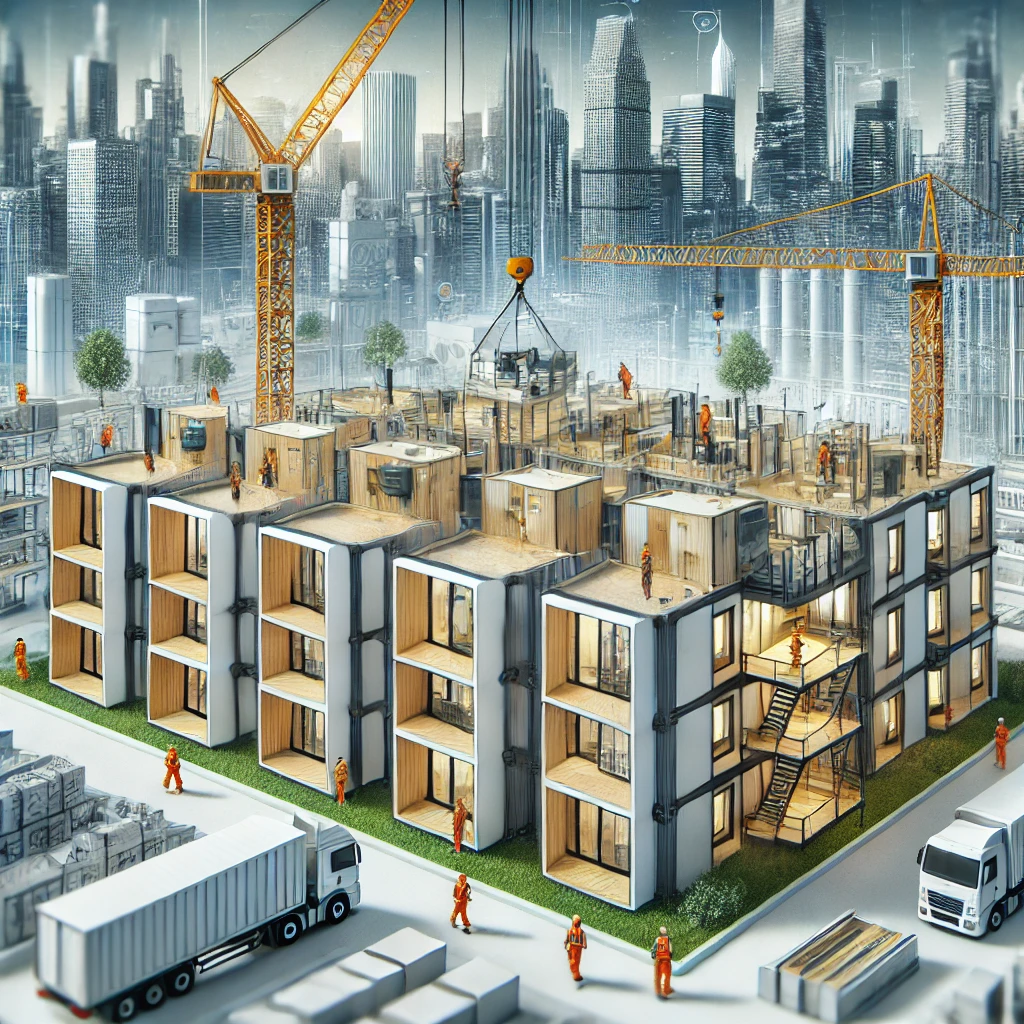
Is Modular the Future of Construction?
The answer is a resounding yes. With urbanization, population growth, and sustainability concerns rising globally, modular construction offers a scalable, efficient, and eco-friendly solution. In markets like Kenya, where affordable housing and rapid urban expansion are critical, modular techniques can meet growing demand.
Even high-end developers are experimenting with modular design, blending luxury with practicality. The fact that modular techniques can replicate everything from sleek modern apartments to sprawling hospitals shows its versatility.
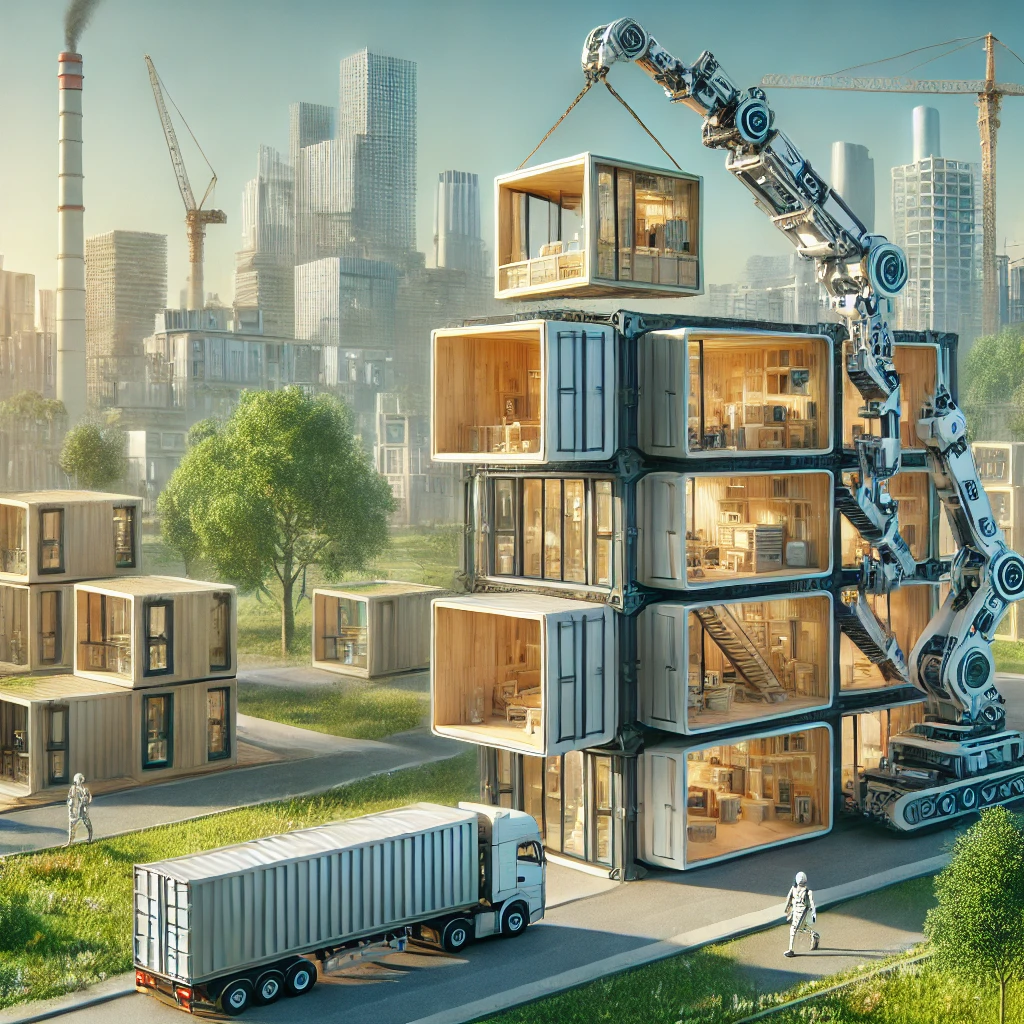
Key Trends to Watch in Modular Construction
If you’re a developer, contractor, or construction enthusiast, keep an eye on these emerging trends:
- Smart Modular Construction: Integration of IoT devices and automation into factory-built modules, enabling energy-efficient and intelligent buildings.
- 3D Printing and Modular Fusion: Factories are starting to use 3D-printed materials for modules, combining cost efficiency with innovative designs.
- Global Adoption: Countries like China, the US, and Sweden are leading in modular adoption, with Africa beginning to embrace this construction style for housing and infrastructure needs.
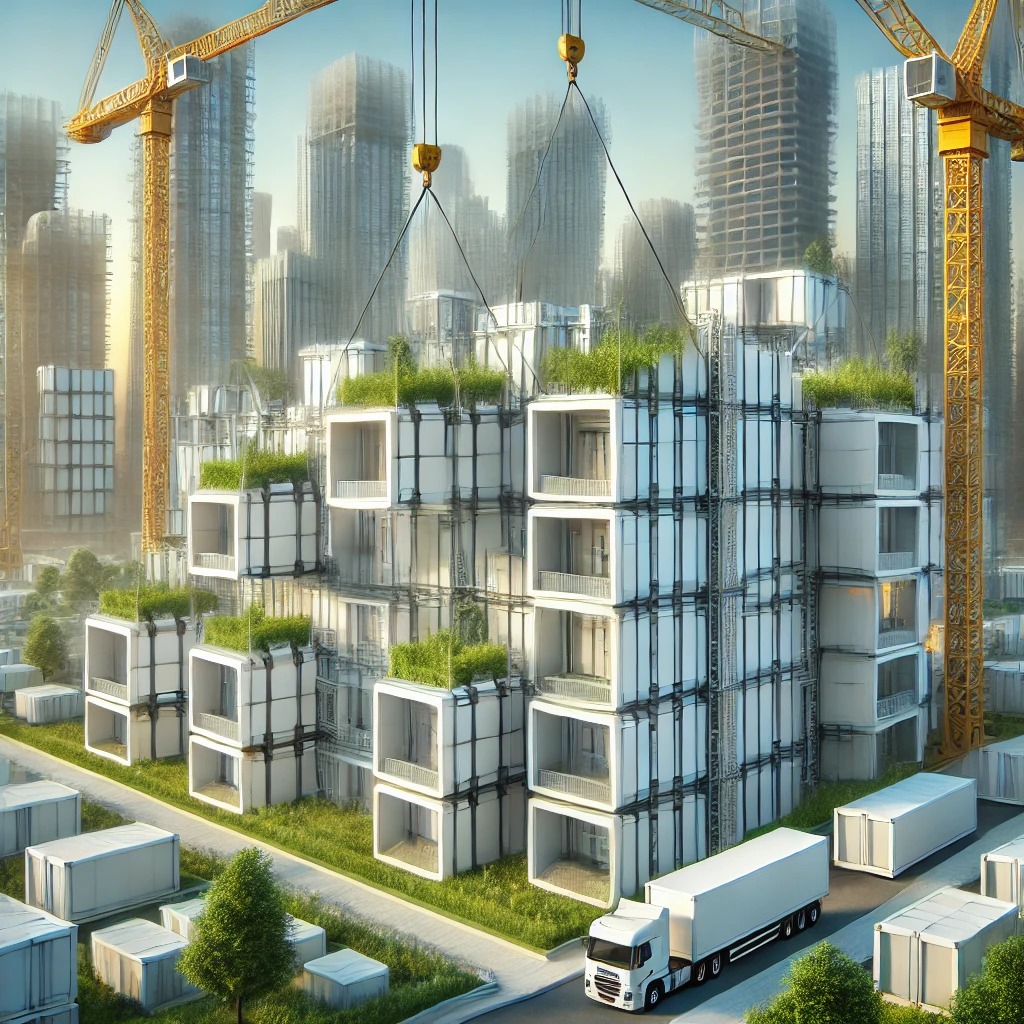
Conclusion
Modular construction isn’t just a trend; it’s a paradigm shift. By marrying technology, efficiency, and sustainability, it has the potential to redefine how we build our cities, homes, and workplaces. The next time you drive past a construction site, don’t be surprised if the building materials arrive fully formed and ready to assemble.
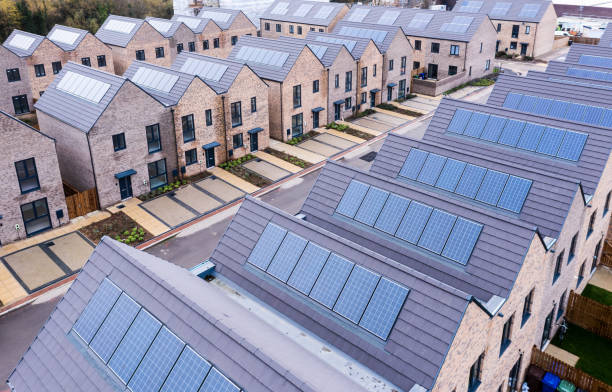
In an industry that thrives on innovation, modular construction might just be the blueprint for the future. So, whether you’re planning your next project or rethinking how construction works, now is the time to explore modular solutions.
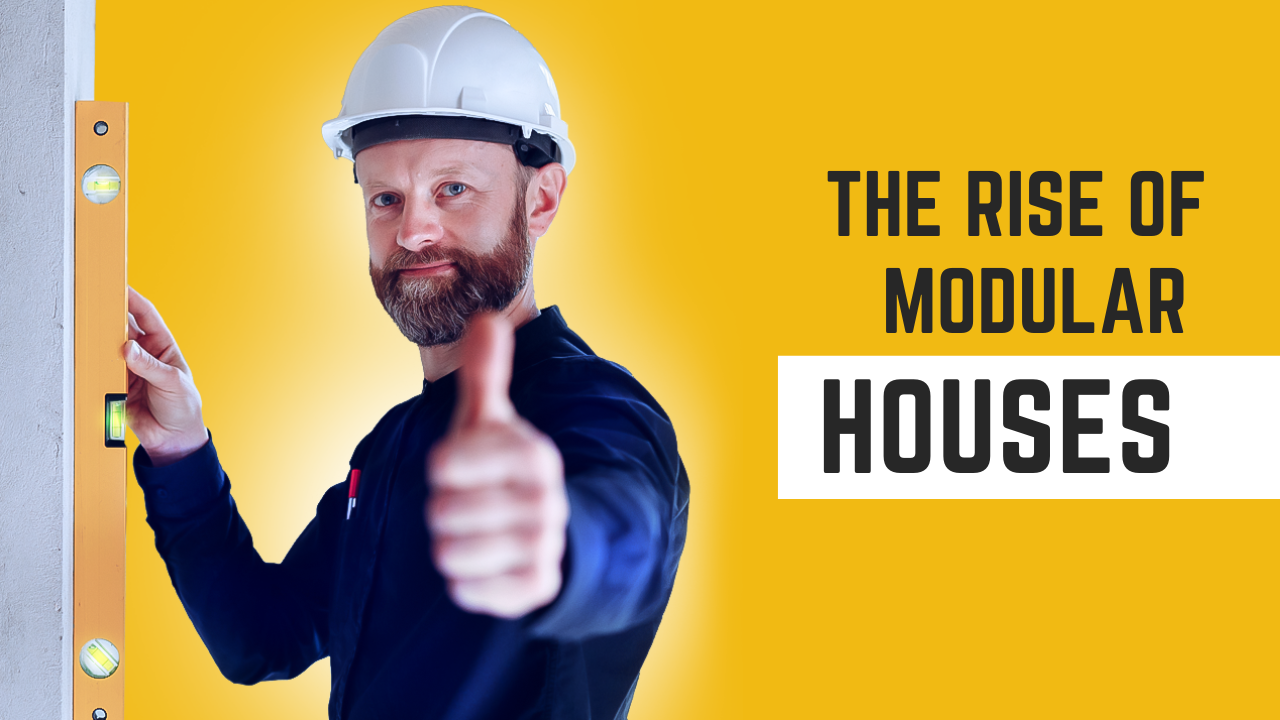
lannybuilders.co.ke
lannybuilders.co.ke